Issues in Testing
Failure #1


The second Generation sleeve arm yielded from the stress caused by the moment created from its offset from the pull rod axis. The following pictures show the oblong hole as a result <note: the black arrow.> Also the "backbone" of the arm should be flat above the sleeve tube <note: the red arrow.> The yield of 6061 T-6 Aluminum is 40 KSI.
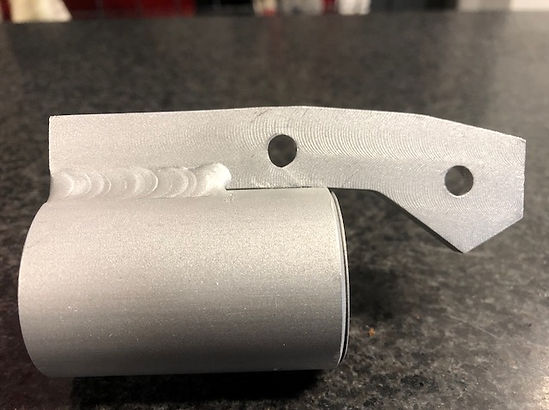
A third generation sleeve and arm was manufactured from steel. The yield strength of 1020 Steel is 50.8 KSI and is 20% stronger than Aluminum. This design remained in tact for the remainder of testing.

This is the whole assembled cutting head.
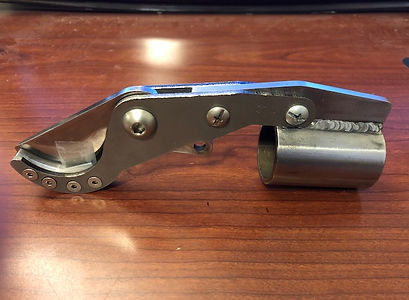
<Note: The steel arm has a distended backbone to account for the bolt hole being so close to the sleeve tube. Also, the TIG weld was continued all the way around the contact plane between the sleeve and arm.>
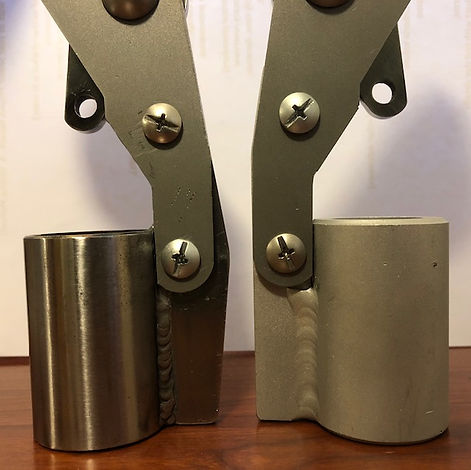
Failure #2
As the 1.25" diameter dry limb tests started, the pull rod yielded to the tension across the cross-sectional area adjacent to the bolt hole. A "necked down" portion was added to the original design to maximize the assembled clearance. After the failure, the neck was deemed unnecessary and a more robust variant was produced. The pull rod was not hardened for the specific purpose of failing before more important (expensive) parts. This failure was premature, with respect to the intended point of failure.
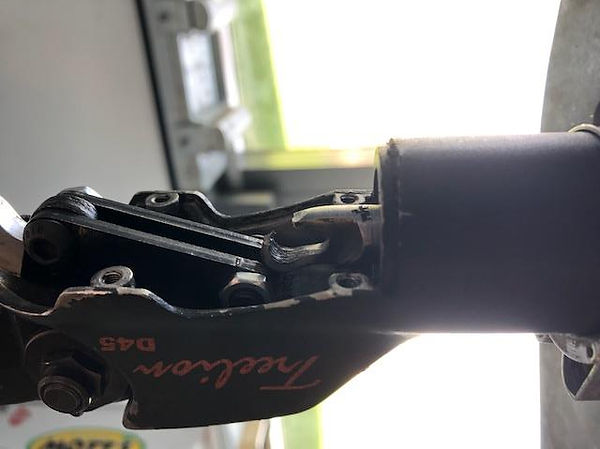
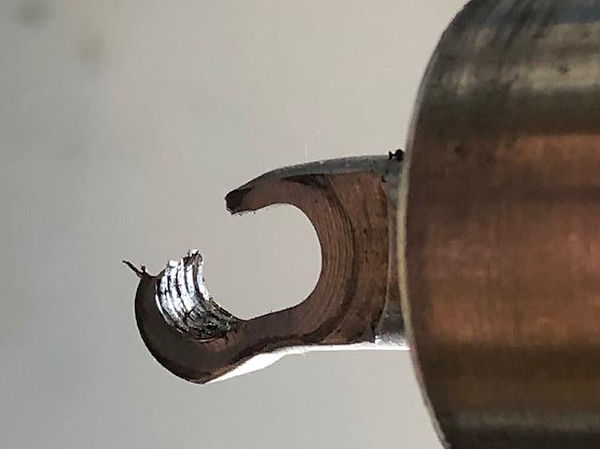
To avoid the odd material impurity as the cause, a second attempt was performed using the backup pull rod. The exact same result occurred.
​
​

Solution: The width of the linkage seat was lengthened with a mill, along the rod until the damaged end could be removed and rounded for clearance. Also, the hole was moved from .125" from the tip, to .1875" away. this was at the limit of clearance for the moving assembly.
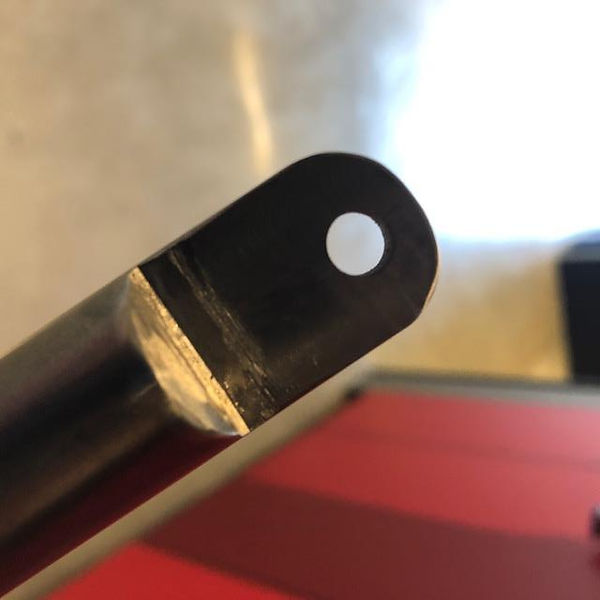
This solution was effective for the remainder of the tests.
Failure #3
The 4130 unhardened steel yielded on both jaws as the first dry 1.75" test was ending. As the following pictures show, the jaws (plain grey) buckled at the stress concentration points (red arrows) due to the yield of the material being 55 ksi. Note: The 2 rear bolt holes are fixed in a concentric manner, between the parts.
The jaws were remade in 4140 pre-hardened plate of the same thickness. This adds 93 KSI yield and does not increase the weight of the jaws. Also, the clearance was re-evaluated to add gusset material below the rear failure sight (green circle). No other additions were made to preserve clearance and weight.
The yield increase alone will prevent buckling at the front point of failure.
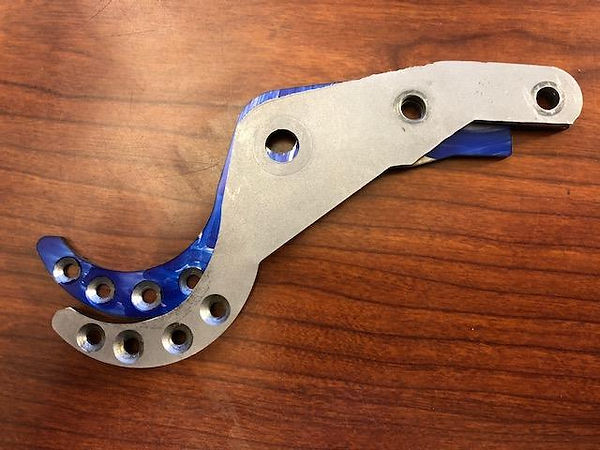
4140 Jaws installed on the head.

Point of buckle and the deflection noted during the test.

This solution was effective and allowed the testing to be completed.
Finished Cutting Head with Upgrade Remanufactured parts.
