A-2 tool steel Blades for the pruning device were heat treated in the ThermoDyne "Thermo Scientific." An installed, EuroTherm 2416 temperature controller was used to complete the heat schedule.
​
The original schedule was researched and followed according to the Black Book of Tool Steel.
​
The second schedule was implemented because the hardness was not adequate for the material recommendations. Further research was done and a comparative schedule was run. The new schedule was gathered from many online blog suggestions that professionals agree is common for A-2 tool steel.


Schedule #1


Between segment 5 and 6, the temperature with respect to time was checked to be within ±5°C of predicted values.
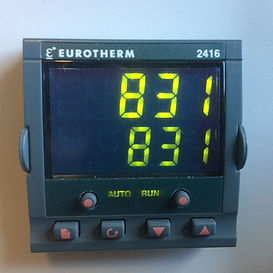
The program containing six segments was entered into the 2416 controller. This began with a ramp to temperature at 171.5 min. And, the program ended with the 30 min. soak at 950°. This furnace was turned off, and then left to naturally cool after the quench.

A second furnace was set at a constant 260°C for the temper segment. This was performed immediately after the quench, from minutes 330 to 490. this furnace was not turned on until the soak began.
Argon gas was used to prevent oxidation in the primary furnace. This facility did not have a prepared source for the argon, so a flow meter and welding supply bottle was used. The ventilation was double checked for safety because argon is oxygen displacing.





Volume flow prevented the insert pipe from damage.

The two original furnaces were close together for convenience. However, they were on the same circuit and immediately popped the breaker. This happened as the soak segment began and caused a ten minute lull in the temperature at soak. The temperature was 920° as the power was restored. Notice that the temperature in this picture was at 954°C, the extra 4° was meant to compensate for the lapse.
​
Furnace #4 was ready and was on a different circuit. So, after the soak temp was restored and the 30 minute minimum was achieved, Furnace #4 was used to perform the 2 hour temper segment.
This is the color of the furnace at 950°C.
Note the argon line entering from just below the Thermocouple in the center of the rear wall.
Heat Treatment Schedule
The Quenching "trough" to hold the hot blades while they cool.
Compressed Air was clamped to the vent hood in such a way, that the restricted flow would surround the blades and not knock them off the trough.



And, into the Temper furnace.


The top blade reached a HRC of 52-53 and the bottom blade reached HRC 54-55. This was lower than the target of 57-60 and will run another heat treat on a better manufactured blade.
Schedule #2
There were five changes made to the heat schedule. Both to standardize the schedule and to increase hardness to the appropriate level of HRC 57-60.
​
-
The Soak temperature was raised to 975°C (1787°F).
-
A metal bucket was used to contain argon (as an anti-carborizer) for the quench.
-
The temper segment temperature was reduced to 180°C (356°F) for increased HRC.
-
The temper was doubled with a low temp. gap and a 2 hr. minimum per segment.
-
A furnace (#3) on a different circuit than the soak furnace (#1) was used for the temper.



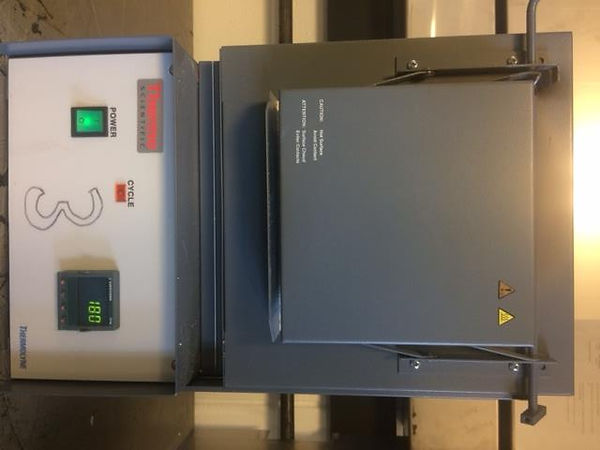
Every other variable was held as closely to the original schedule as possible in order to be directly compared. For instance, Pre-heat time to temp., argon injection, quench temp. and material.
The HRC was measured to be in a range of 56-58. This is within the acceptable range for the recommended hardness for the A-2 Tool steel used as a cutting blade.
