The jaws and blade "blank" outlines were laser cut and the hole centers etched. A secondary process was used to drill, ream, countersink and tap the finished holes.
​
​
​
The variable rake angles on the blade were achieved by superimposing the line of the shoulder onto the blank. Then, the blank was ground to the center-line of the marked cutting edge. The 1:1 drawing below was used as the stencil.
Manufacturing
Jig assembly and sleeve arm welding credit: Matt Burvey
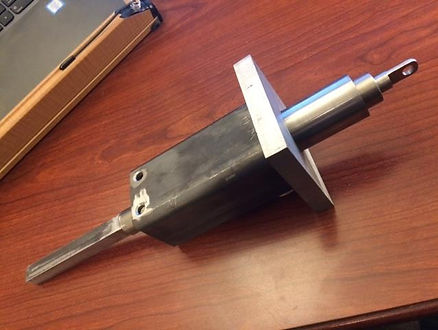
First Generation Sleeve Parts
<Notice Flat surface on the exterior face on the tube where arm will mate.>
The following pictures and descriptions are in a chronological order. The outsourced processes are noted as the materials were turned over. Drawing schematics can be viewed in the Analysis tab above.
Milling the Pull Rod for the testing Jig was the first process.

Jig will fit directly into Tinius-Olsen tensile tester and accommodate both cutting systems. A direct comparison will be made. The original cutting head is shown here.
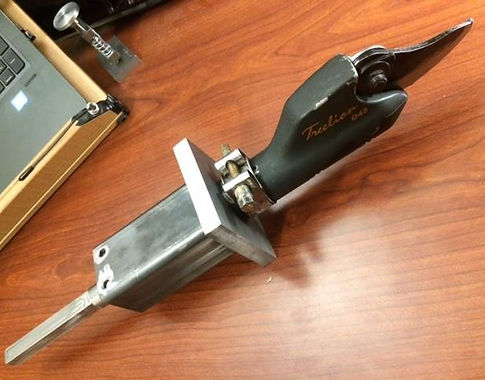
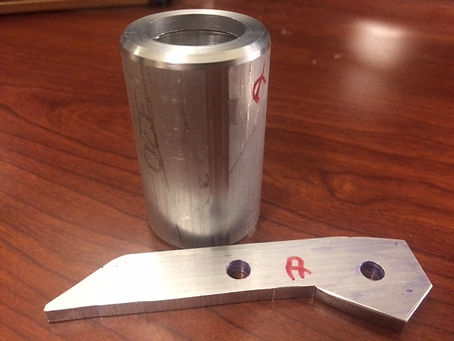
Pre-TIG Sleeve

Pre-weld Mock-up in position.
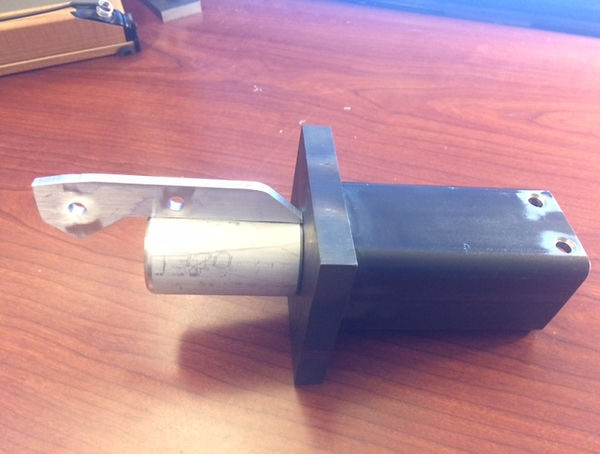
A thumbscrew was added to hold the head onto the testing device. A split with clamp could easily be substituted as a functional option. The Pellenc has the split/clamp style.


The media blasting booth was used on all non-mating surfaces.
​
​
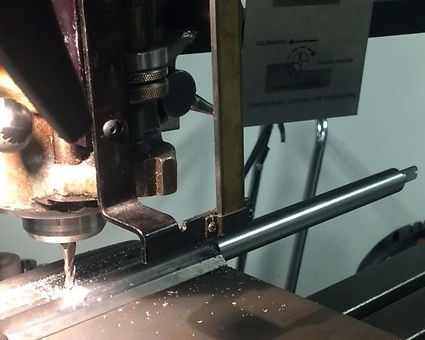
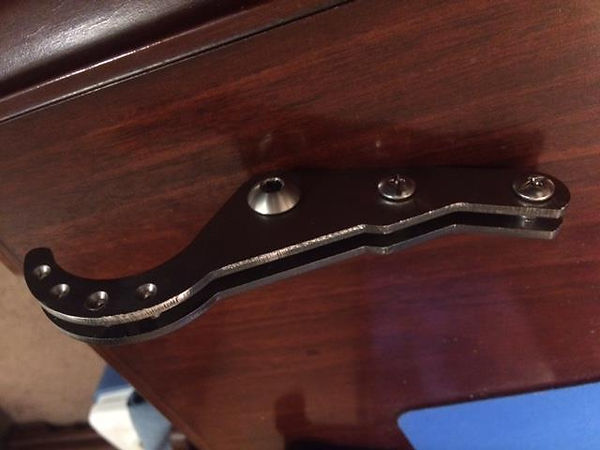
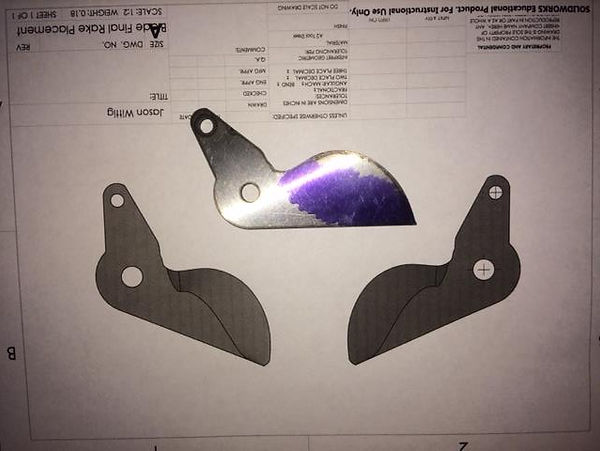

After the Heat Schedule was completed, the blade was sharpened to a fine finish with an Arkansas Stone and a spray lubricant for chip removal.
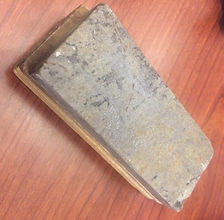
The edge was roughed in with a bench grinder and then finish ground with a flat file.
Following the heat treat schedule, the surface finish was polished with jewelers rouge and a cloth wheel.

This is an aborted attempt to mass produce the variable rake angle. A cam that is turned by hand raises the angle as the blade is turned from the center line. This is a complete and different project that is outside of the scope of my project. However, Knecht industries makes a similar advanced tools for this purpose. https://www.knecht.us/products/grinding-machines/for-cutter-knives/s-200/
​


Precision WaterJet of Wenatchee was also commissioned to cut the flat aluminum parts. These parts were "tabbed" into the plate to prevent them from falling into the water tank. <Note the inclusion of second Generation sleeve arm.>
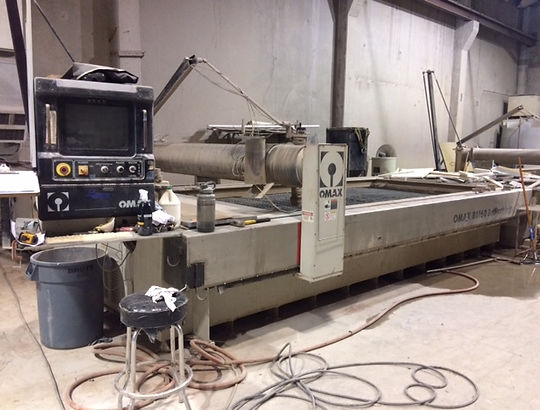
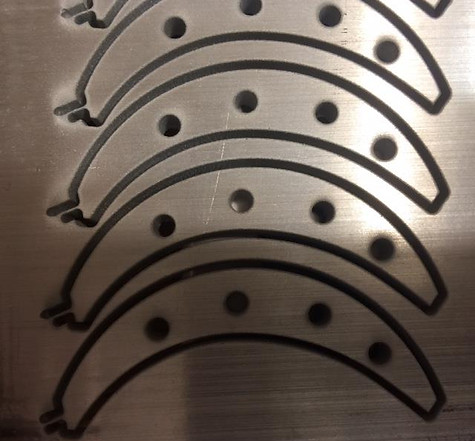

Center anvil is polished drilled and installed. Note that the holes were cut undersized for the specific purpose of match drilling it to the jaws.
​
HFHauff produced a machined version of the center anvil that is used in the "display only" cutting head. The finish is much finer and aesthetically better.
Finished Cutting Head
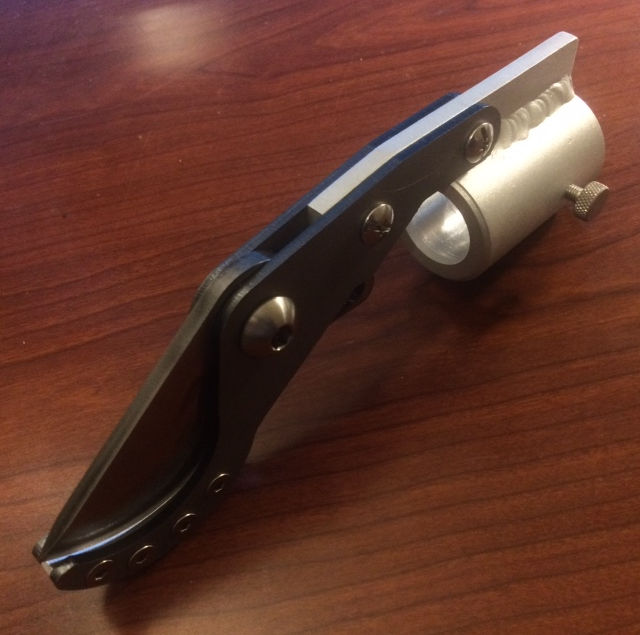